Insights from Stellantis and Mazda
In our quest for a greener future, the automotive industry is making remarkable strides toward reducing emissions in its manufacturing operations. We caught up with experts from Stellantis and Mazda to delve into their adoption of circular economy principles in vehicle production, an approach that’s at the forefront of eco-friendly innovation.
Undoubtedly, decarbonizing vehicles is paramount for countries striving to achieve net-zero emissions. While electric vehicles (EVs) are hailed as a game-changer, the move to electrification alone, while eliminating tailpipe emissions, may not be the silver bullet for creating a genuinely eco-conscious auto industry. Surprisingly, data from the International Energy Agency (IEA) reveals that the average CO2 emissions generated during the production of battery electric vehicles still amount to a hefty 5.4 tonnes.
This is where the adoption of circular economy principles in manufacturing comes into play and could significantly slash these numbers. Natalia Dziergwa, Circular Cars Initiative Specialist at the World Economic Forum, rightly points out that addressing emissions across the entire value chain is crucial for a low-carbon mobility system. Material circularity and lifetime optimization are pivotal in this transition, ranging from using low-carbon materials to extending a product’s life through practices like reuse, remanufacturing, and refurbishment.
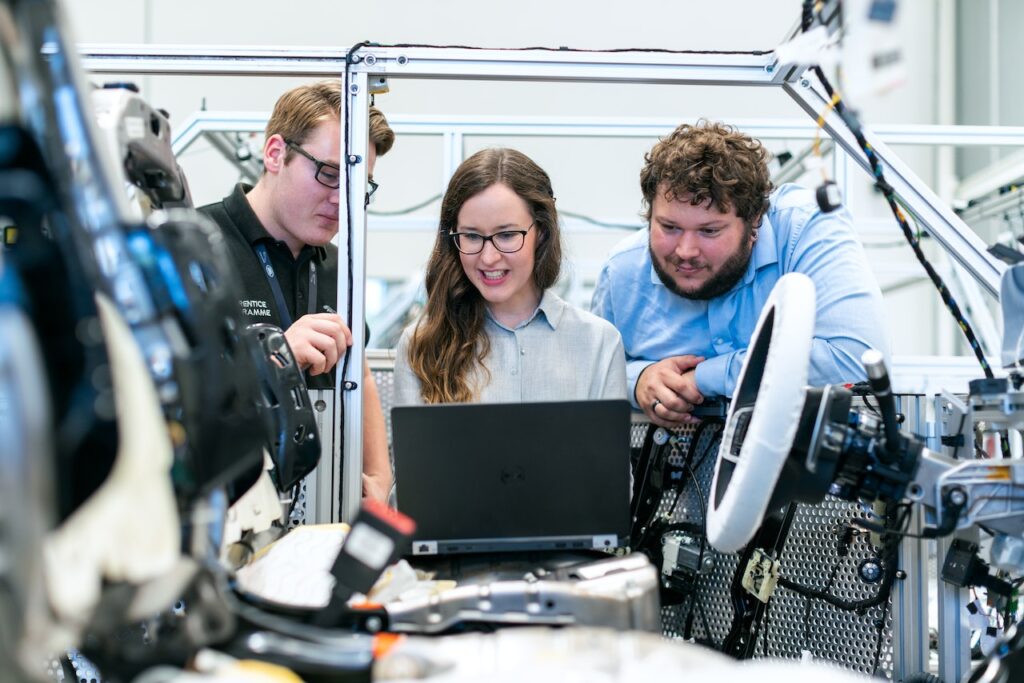
Stellantis is setting an example by dedicating an entire business unit to circular economy principles, signaling its commitment to reducing the environmental footprint of its factories worldwide. This initiative aligns perfectly with Stellantis’s ambitious goal of achieving carbon neutrality by 2038. The essence of the circular economy model is moving away from the traditional “take-make-dispose” approach toward resource circularity, where materials and products enjoy an extended lifespan, waste is minimized, and the demand for fresh raw materials decreases. One of the ways Stellantis achieves this is by designing vehicle components that are easy to disassemble and recycle, repurposing production scraps, and remanufacturing defective parts.
Mazda, another forward-thinking automaker, has set its sights on a carbon-neutral future, aiming to make all its production facilities carbon-neutral by 2035 and achieve carbon neutrality across its entire business by 2050. Their strategy focuses on energy conservation, adopting renewable energy sources, and introducing carbon-neutral fuels. Furthermore, Mazda is actively exploring the integration of circular economy principles within its production processes. Their objective is to enhance recyclability in vehicle design, simplify dismantling and separation processes, and incorporate easily recyclable plastics.
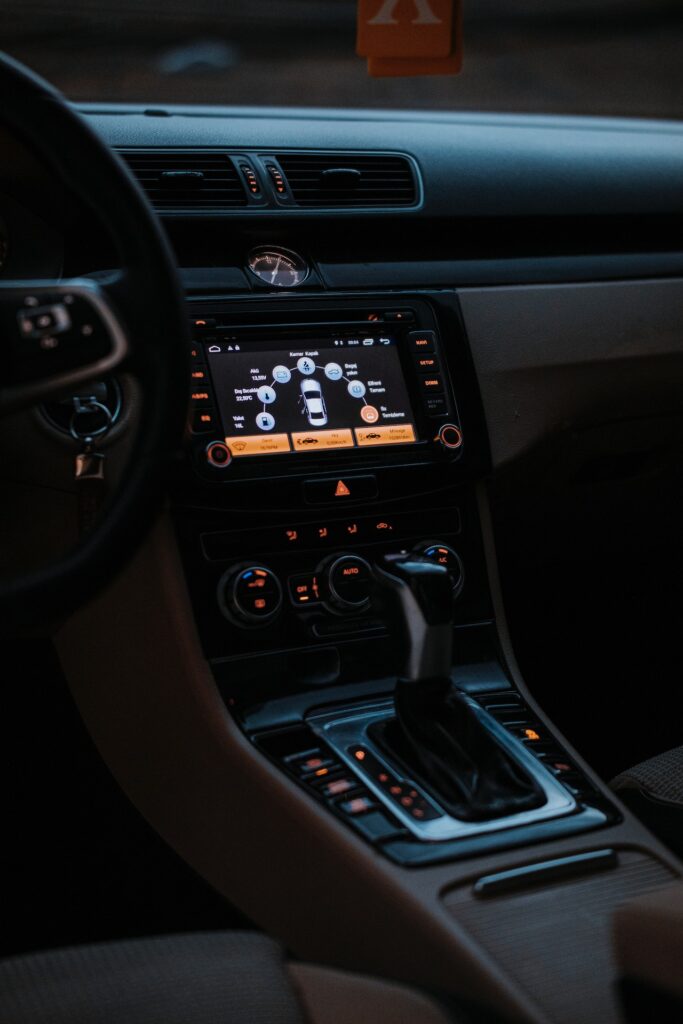
Both manufacturers acknowledge the significance of circular economy principles in mitigating emissions. However, they recognize that there are challenges, particularly concerning the degradation of materials, a crucial aspect when dealing with electric vehicles. Even though reusing EV batteries is essential, as they age, their capacity and efficiency decrease, rendering them unsuitable for vehicular use. Instead, these batteries can find a second life in applications such as energy storage and power generation, highlighting the need for skilled labor forces in circular economy production.
In conclusion, embracing circular economy principles is not only environmentally responsible but also essential for the automotive industry’s sustainability. Collaboration across the industry and value chain is pivotal. Together, we can transform the automotive landscape into a truly circular and eco-conscious sector. For those keen on contributing to a sustainable future and looking for expert solutions in end-of-life vehicle disposal and recycling, visit scrap my car where your actions matter.